Ball valve pneumatic actuators are critical components in modern fluid control systems, offering precise and reliable operation in demanding industrial environments. This article explores the design principles, operational mechanisms, and key applications of pneumatic actuators paired with ball valves, emphasizing their advantages in automation, safety, and efficiency.
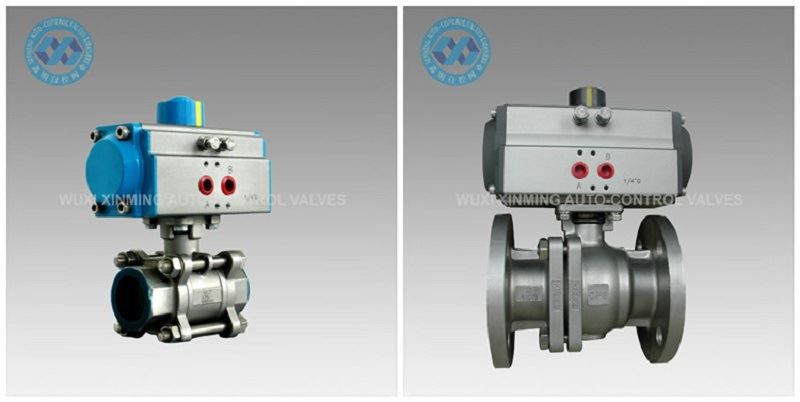
1. Introduction
Ball valves are widely used in industrial pipelines for their robust sealing capabilities, low torque requirements, and bidirectional flow control. When integrated with pneumatic actuators, these valves become essential for automated systems requiring rapid response, high cycle rates, and fail-safe operation. Pneumatic actuators convert compressed air energy into mechanical motion, enabling remote or programmed control of ball valve positions (open, closed, or modulated).
2. Design and Components of Pneumatic Actuators
A pneumatic actuator for ball valves typically comprises the following components:
- Actuator Housing: Constructed from aluminum, stainless steel, or engineered polymers to withstand harsh environments.
- Piston or Diaphragm: Translates air pressure into linear or rotary motion.
- Spring Mechanism: Provides fail-safe operation (e.g., spring return to open/close positions during air supply failure).
- Shaft and Linkage: Connects the actuator to the ball valve stem, transmitting torque.
- Position Indicator: Visual or electronic feedback on valve position.
- Air Ports: Inlet/outlet ports for compressed air supply.
Actuators are categorized into two types:
- Double-Acting: Uses air pressure to drive movement in both directions (open and close).
- Single-Acting (Spring-Return): Compressed air moves the valve in one direction, while a spring returns it to the default position.
3. Working Principle
Pneumatic actuators operate on the principle of differential pressure. Compressed air (typically 4–7 bar) is directed into the actuator chamber, forcing the piston or diaphragm to move. This motion is converted into a 90° rotational movement (for quarter-turn ball valves) via a rack-and-pinion or scotch yoke mechanism. Key performance metrics include:
- Torque Output: Matched to valve size and system pressure requirements.
- Speed: Adjustable via flow control valves to regulate air supply.
- Positioning Accuracy: Enhanced with accessories like positioners or limit switches.
4. Key Advantages
- Rapid Response: Compressed air enables faster actuation compared to electric or hydraulic alternatives.
- Explosion-Proof: Ideal for hazardous areas (e.g., oil and gas) due to absence of electrical components.
- Low Maintenance: Minimal wear parts and resistance to overload conditions.
- Fail-Safe Capability: Spring-return designs ensure safe shutdown during emergencies.
- Scalability: Compatible with positioners, solenoid valves, and PLCs for advanced automation.
5. Industrial Applications
Ball valve pneumatic actuators are deployed across industries requiring precise flow control:
- Oil & Gas: Shut-off and isolation in pipelines, refineries, and LNG facilities.
- Chemical Processing: Corrosion-resistant actuators handle aggressive media.
- Water/Wastewater: Automated control in treatment plants and distribution networks.
- Pharmaceutical: Hygienic designs for sterile processing.
- Power Generation: Steam, cooling water, and fuel line management.
6. Selection Criteria
Choosing the right actuator involves evaluating:
- Valve Torque Requirements: Determined by valve size, pressure class, and fluid viscosity.
- Air Supply Availability: Pressure range and air quality (e.g., filtered, lubricated).
- Environmental Conditions: Temperature extremes, corrosive atmospheres, or explosive zones.
- Standards Compliance: ISO 5211 (mounting interface), ATEX/IECEx (hazardous area certification), and NAMUR (industrial automation compatibility).
7. Emerging Trends
- Smart Actuators: Integration with IoT for predictive maintenance and real-time diagnostics.
- Energy Efficiency: Reduced air consumption via precision control systems.
- Lightweight Materials: Advanced composites for high strength-to-weight ratios.
8. Conclusion
Ball valve pneumatic actuators remain indispensable in industrial automation, combining reliability, speed, and adaptability. Engineers must prioritize proper sizing, material compatibility, and adherence to industry standards to optimize performance in critical applications.
If you want to learn more about low-priced products, please visit the following website: www.xm-valveactuator.com